Introduction
3D printing has revolutionized the way products are designed, prototyped, and manufactured. With a wide range of 3D printing processes available, it can be challenging to determine which one is the best fit for your specific product development needs. In this comprehensive guide, we will explore the various 3D printing processes and provide insights to help you make an informed decision. Whether you are looking to create intricate prototypes, functional parts, or even production-ready components, understanding the strengths and limitations of each process is crucial. So, let's delve into the world of 3D printing and discover how to choose the right process for your product development journey.
Stereolithography (SLA)
Stereolithography is a popular 3D printing process that uses liquid resin and a UV laser to create highly detailed and accurate parts. SLA is well-suited for producing prototypes, intricate models, and parts with smooth surface finishes. However, it may not be the best choice for large-scale production or parts that require high mechanical strength.
Selective Laser Sintering (SLS)
Selective Laser Sintering utilizes a laser to fuse powdered materials, such as nylon or polyamide, into solid objects. SLS is known for its versatility, allowing the creation of functional prototypes, complex geometries, and parts with good mechanical properties. It is particularly suitable for producing parts with intricate internal structures or for low-volume production runs.
Fused Deposition Modeling (FDM)
Fused Deposition Modeling is one of the most widely used 3D printing processes. It works by extruding thermoplastic filament layer by layer to create a 3D object. FDM is known for its affordability, ease of use, and ability to produce functional prototypes and durable parts. However, the surface finish may not be as smooth as other processes, and the strength can vary depending on the material used.
Digital Light Processing (DLP)
Digital Light Processing is similar to SLA but utilizes a different light source, such as a digital projector, to cure liquid resin. DLP offers faster print speeds compared to SLA and is suitable for creating detailed prototypes and models. However, the surface finish may not be as smooth, and the material options can be more limited.
Direct Metal Laser Sintering (DMLS)
Direct Metal Laser Sintering is a process that uses a high-powered laser to selectively fuse metal powders, producing fully dense metal parts. DMLS is ideal for creating complex metal components with excellent mechanical properties and high precision. It is commonly used in industries such as aerospace, automotive, and healthcare. However, the high costs and longer production times associated with DMLS make it more suitable for specialized applications.
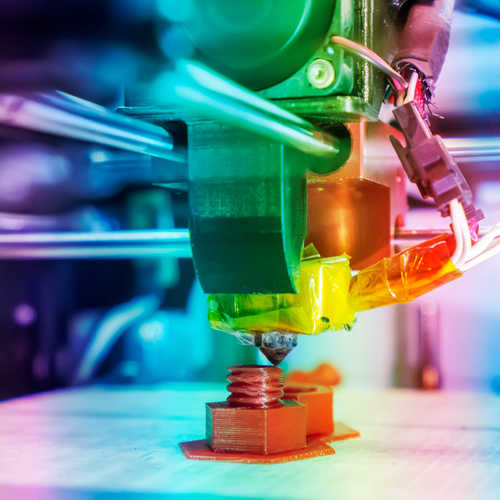
Conclusion
When choosing the right 3D printing process for your product development needs, consider factors such as the desired level of detail, mechanical properties, surface finish, material availability, production volume, and budget. Each 3D printing process has its strengths and limitations, making certain processes more suitable for specific applications than others. By understanding the characteristics of different processes like Stereolithography, Selective Laser Sintering, Fused Deposition Modeling, Digital Light Processing, and Direct Metal Laser Sintering, you can make an informed decision that aligns with your project requirements. Embrace the power of 3D printing and unlock the endless possibilities it offers for your product development journey.